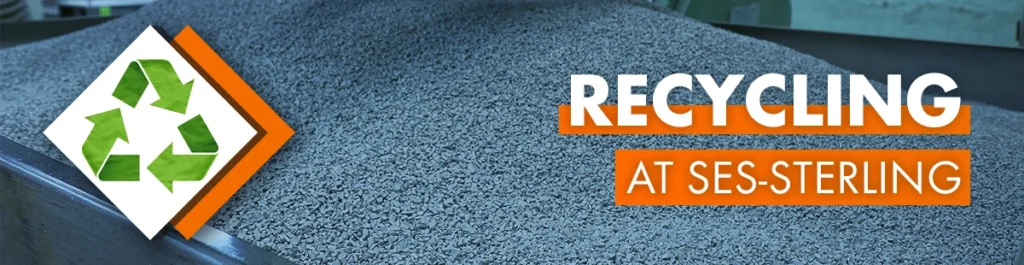
What if industrial waste could be reintegrated into the production chain? For some years now, the recycling and reuse of waste has been shaping the future of industry.
At SES-STERLING, these environmentally-friendly processes are already well established on the production floor. Take a behind-the-scenes look at our commitment to a greener, more sustainable industry.
Plastic waste: an environmental issue
Plastic is one of the most polluting materials in the world. This raw material only begins to disintegrate after 100 years. The stakes are so high that the plastics industry federation has committed itself to making a major contribution to the goal of 100% recycled plastic by 2025.
At SES-STERLING, our overall annual consumption of plastic materials is more than 2,000 tonnes, which results in more than 500 tonnes of production waste per year. Recycling is therefore a key priority.
What are the stages of plastic recycling?
With more than 4 800 km of cable trunking produced per year, we use no less than 1400 tonnes of PVC, which results in almost 400 tonnes of production waste. During the manufacture of a cable duct, the material is extruded into a finished product. This manufacturing process generates nearly 30% of waste from the profile punching stage. The reuse of offcuts after grinding has been a necessity from the start of the business.
All these offcuts are recovered and sorted in order to be crushed and then reused for the manufacture of new products. Contrary to popular belief, the recycling process does not alter the quality and properties of the material. With the recycling process at SES-STERLING, the material is given a second life to produce a new quality product, whose technical properties are maintained, while protecting the environment.
More than just recycling cable ducts!
At SES-STERLING, it is not only plastic that is recycled. Everything is thought out and studied so that recycling is an integral part of the production process of each product. The concept of recycling is integrated at an early stage, right from the product development process. Here are some examples.
Injection moulded parts:
These are manufactured on specific production machines which allow the recovery of every scrap material caused by the injection process. Within the same machine, the offcuts are directly crushed and automatically re-injected to be used in the manufacture of a new product. 100% of the off-cuts are used in this way.
PLIO® flexible PVC sleeves:
Even flexible plastic is recycled at SES-STERLING. A rigorous sorting by quality of scrap is carried out. These offcuts are then crushed and processed for the manufacture of new sleeves. Here again, expert control of the recycling procedure ensures that the quality of the product is not altered.
The MORE label: active participation in the circular economy
The circular economy aims to reduce the consumption of natural resources and minimise waste by recycling materials. By reusing our production off-cuts and buying back raw materials from other manufacturers throughout the year, we actively participate in this process.
In November 2024, we obtained the MORE label awarded by POLYVIA (union of polymer processors). This label is a real recognition of our commitment and our role in participating in the circular economy. We are MObilised to REcycle.
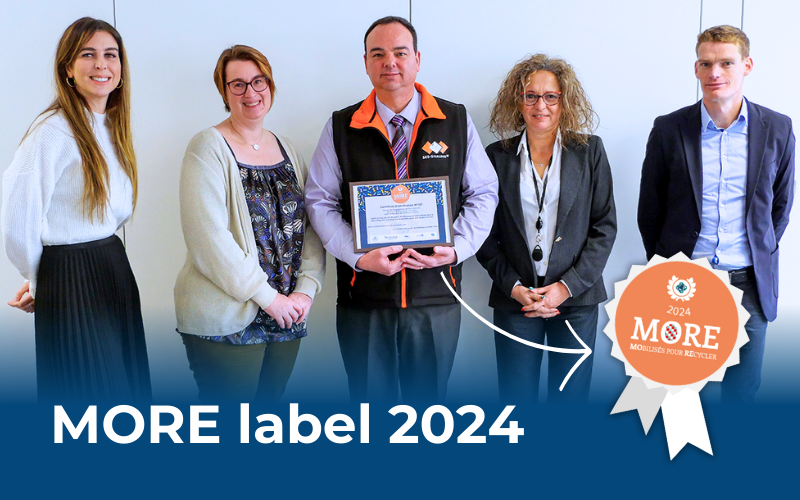
To find out more about our commitment
SES-STERLING’s commitment to the environment is not limited to waste recycling. Every day, our teams participate in the development of a greener, more sustainable industrial model.
Discover the latest addition to the world of eco-friendly fasteners and fixings: the biodegradable SES-QUICK BIO cable tie from SES-STERLING. 🌱
Through simple gestures or major transformations, we are working actively and continuously to reduce our environmental footprint. To find out more about our commitments and values, see our CSR Commitments section.